表面処理の選択は、すべての設計者が直面する問題です。利用可能な表面処理オプションにはさまざまな種類があり、高レベルの設計者は、設計の経済性と実用性を考慮するだけでなく、組み立てプロセスや環境要件にも注意を払う必要があります。以下に、ファスナーの専門家が参照できるように、上記の原則に基づいてファスナーに一般的に使用されるコーティングをいくつか簡単に紹介します。
1.電気亜鉛メッキ
亜鉛は、商業用ファスナーに最も一般的に使用されるコーティングです。価格も比較的安く、見た目も良いです。一般的な色には黒とミリタリーグリーンがあります。ただし、耐食性能は平均的であり、亜鉛メッキ(コーティング)層の中で最も耐食性能が低いものとなります。一般に、亜鉛メッキ鋼板の中性塩水噴霧試験は 72 時間以内に実施されますが、中性塩水噴霧試験を 200 時間以上継続するためには特殊なシーリング剤も使用されます。ただし、価格は通常の亜鉛メッキ鋼板の5~8倍と高価です。
電気亜鉛メッキのプロセスは水素脆化を起こしやすいため、グレード 10.9 を超えるボルトは通常亜鉛メッキで処理されません。めっき後にオーブンを使用して水素を除去することも可能ですが、60℃以上の温度では不動態皮膜が損傷するため、電気めっき後、不動態化の前に水素除去を行う必要があります。これでは操作性が悪く、処理コストも高くなります。実際には、一般的な製造工場では、特定の顧客からの指示がない限り、積極的に水素を除去することはありません。
亜鉛メッキファスナーはトルクと予締め力の均一性が悪く不安定なため、重要部品の接続には一般的に使用されません。トルク予圧の安定性を向上させるために、めっき後に潤滑剤を塗布する方法もあり、トルク予圧の安定性を向上・向上させることができる。
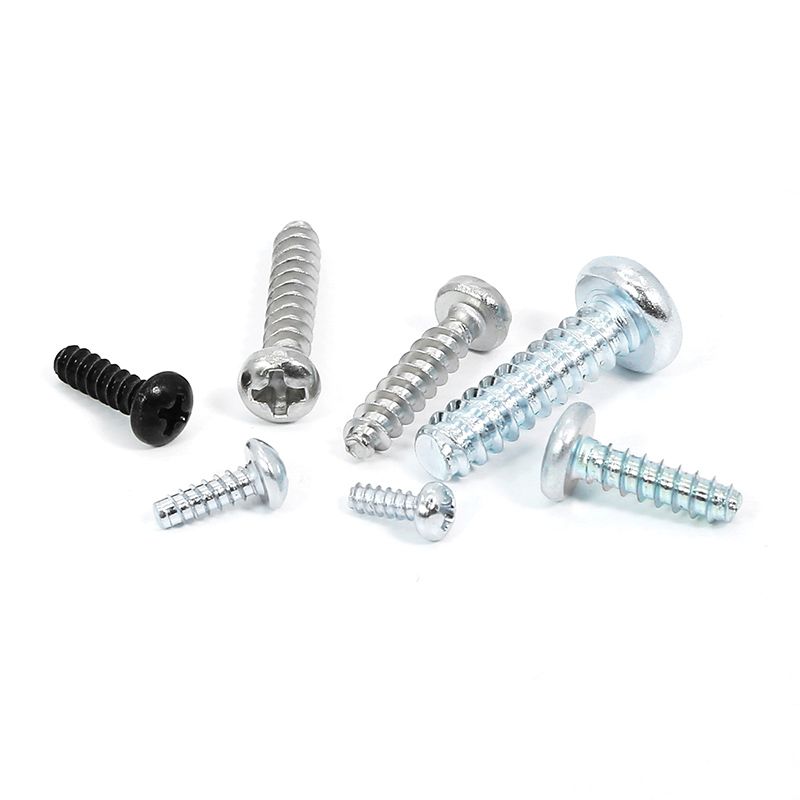
2. リン酸塩処理
基本的な原理として、リン酸塩処理は亜鉛めっきよりも比較的安価ですが、耐食性は亜鉛めっきよりも劣ります。リン酸塩処理後は油を塗布する必要があり、耐食性は塗布した油の性能と密接に関係します。例えば、リン酸塩処理後、一般の防錆油を塗布し、中性塩水噴霧試験を10~20時間だけ実施します。高級防錆油の塗布には最大 72 ~ 96 時間かかる場合があります。ただし、価格は一般的なリン酸塩の2~3倍です。
ファスナーに一般的に使用されるリン酸塩処理には、亜鉛系リン酸塩処理とマンガン系リン酸塩処理の 2 種類があります。亜鉛系リン酸塩処理はマンガン系リン酸塩処理よりも潤滑性能に優れ、マンガン系リン酸塩処理は亜鉛めっきよりも耐食性、耐摩耗性に優れています。華氏225〜400度(107〜204℃)の温度範囲で使用できます。特にいくつかの重要なコンポーネントの接続に使用されます。エンジンのコンロッドボルト・ナット、シリンダーヘッド、メインベアリング、フライホイールボルト、ホイールボルト・ナットなど。
高強度ボルトにはリン酸塩処理が施されており、水素脆化の問題も回避できます。そのため、工業分野ではグレード10.9以上のボルトにはリン酸塩処理が一般的です。
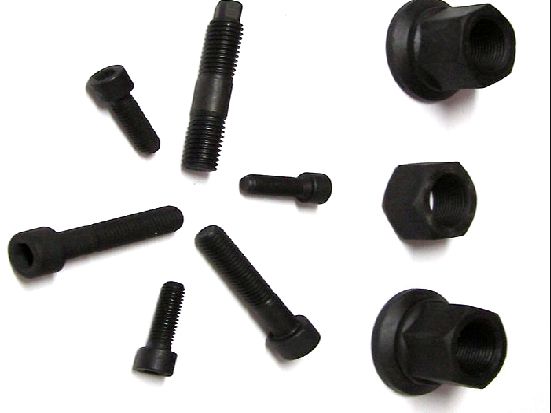
3. 酸化(黒ずみ)
黒染め+油引きは最も安価で燃費も良く見た目も良いことから工業用ファスナーのコーティングとして人気です。黒く変色しているため防錆力はほとんどなく、油を塗っていないとすぐに錆びてしまいます。油が存在する場合でも、塩水噴霧試験は 3 ~ 5 時間しか持続できません。
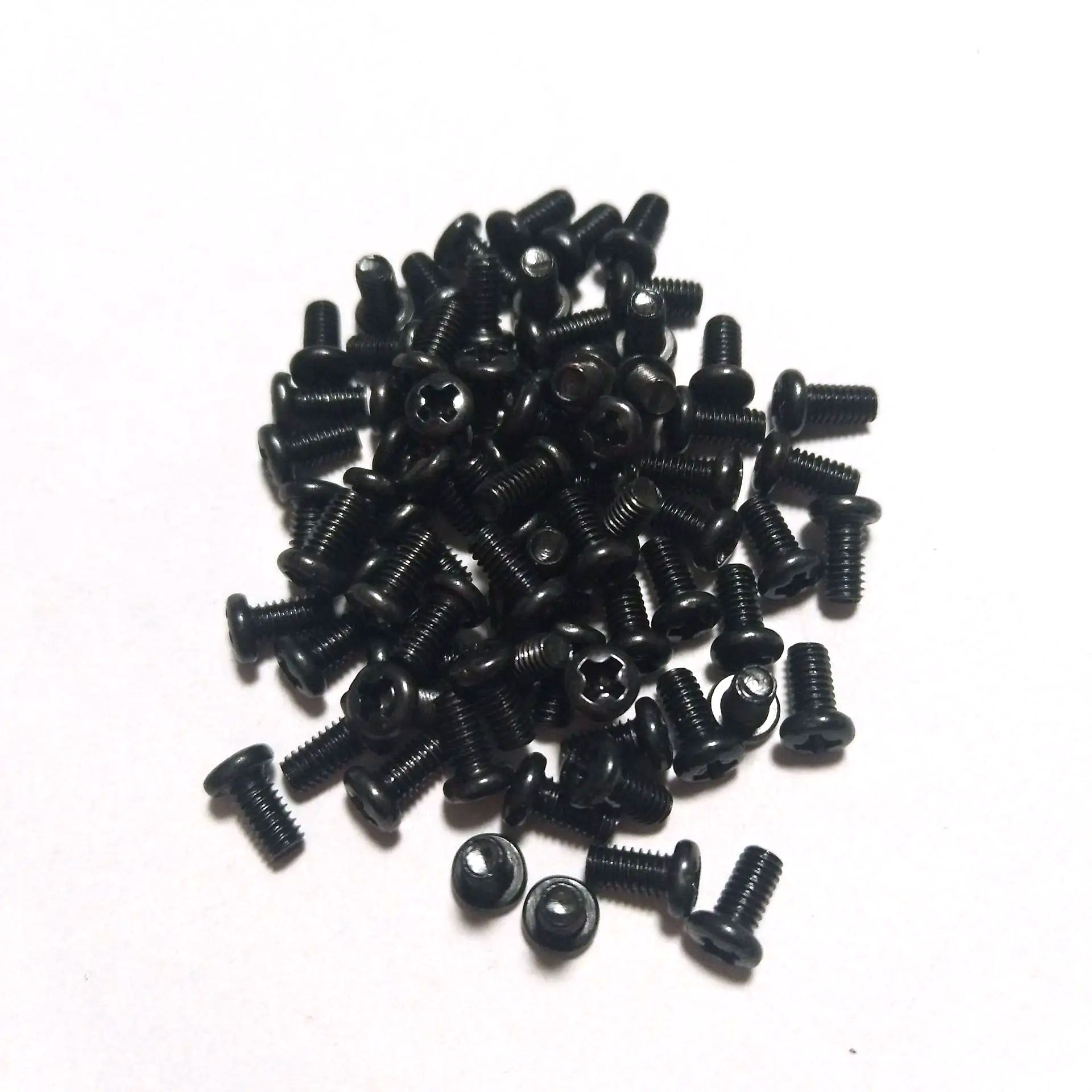
4. 電気メッキ隔壁
カドミウムめっきは、他の表面処理と比較して、特に海洋大気環境において優れた耐食性を持っています。カドミウム電気めっきの工程における廃液処理コストは高く、その価格は電気亜鉛めっきに比べて15~20倍程度です。したがって、一般的な産業では使用されず、特定の環境でのみ使用されます。石油掘削プラットフォームやHNA航空機に使用されるファスナー。
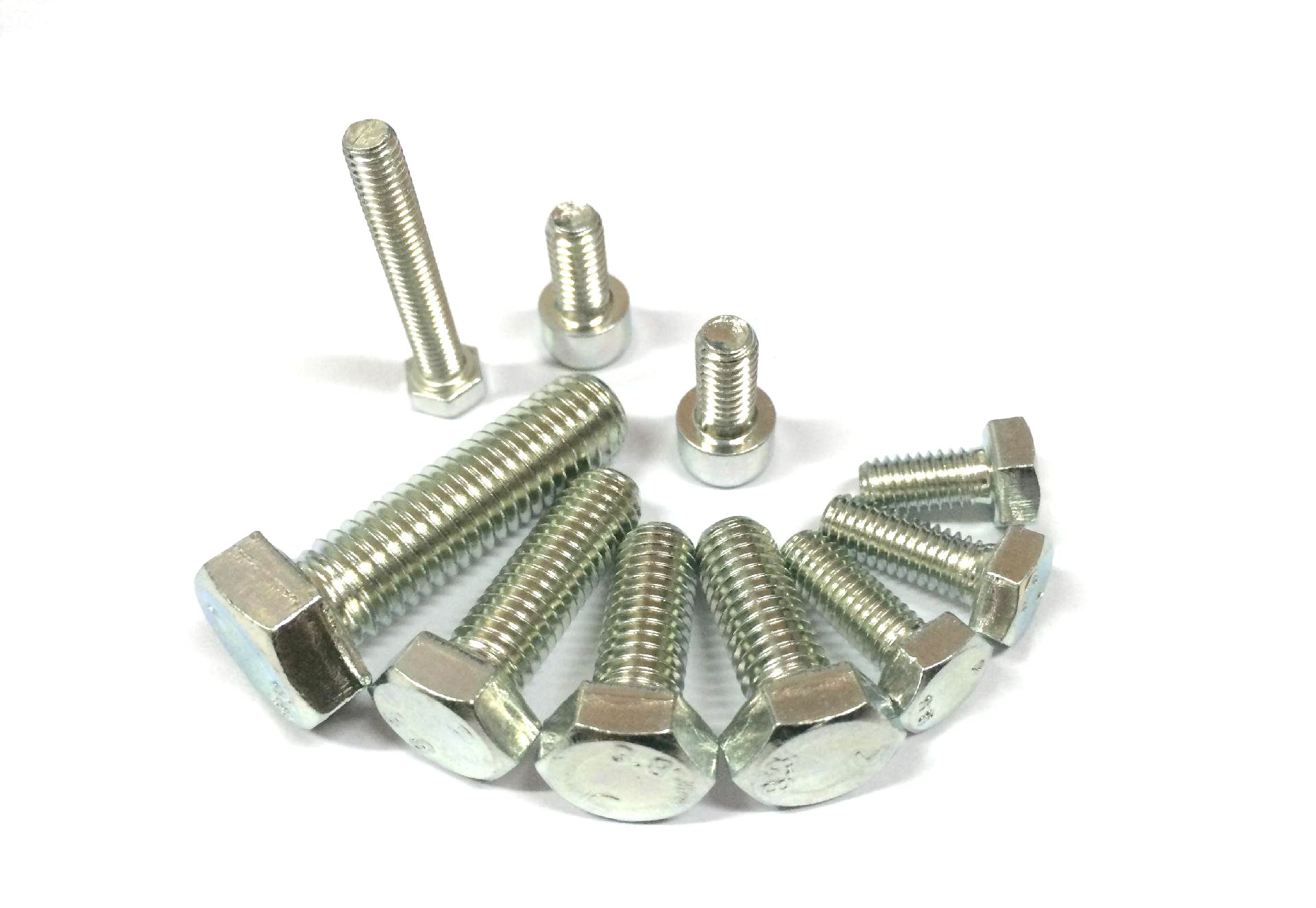
5.クロムメッキ
クロムコーティングは大気中で非常に安定しており、色が変化したり光沢が失われたりしにくく、硬度が高く、耐摩耗性に優れています。ファスナーへのクロムメッキの使用は、一般に装飾目的で使用されます。良質なクロムメッキファスナーはステンレス鋼と同じくらい高価であるため、高い耐食性が要求される産業分野ではほとんど使用されません。ステンレスでは強度が不足する場合に限り、クロームメッキの留め具を使用します。
腐食を防ぐために、クロムめっきの前に銅とニッケルをめっきする必要があります。クロムコーティングは華氏1200度(650℃)の高温に耐えることができます。しかし、電気亜鉛メッキと同様に水素脆化の問題もあります。
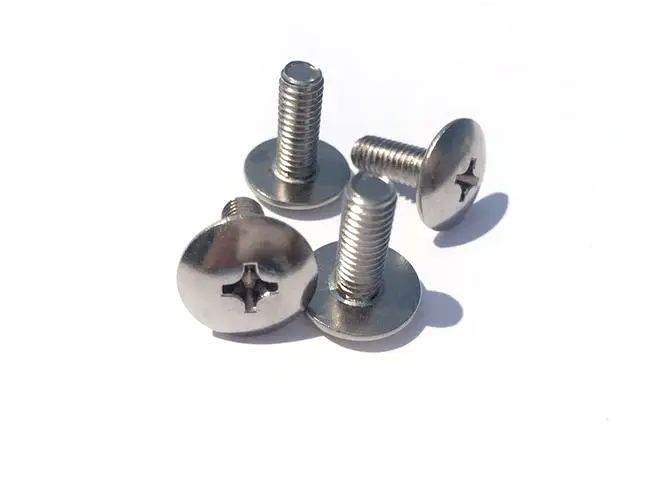
6. ニッケルメッキ
主に耐食性と良好な導電性の両方が必要な領域に使用されます。たとえば、車両バッテリーの出力端子などです。
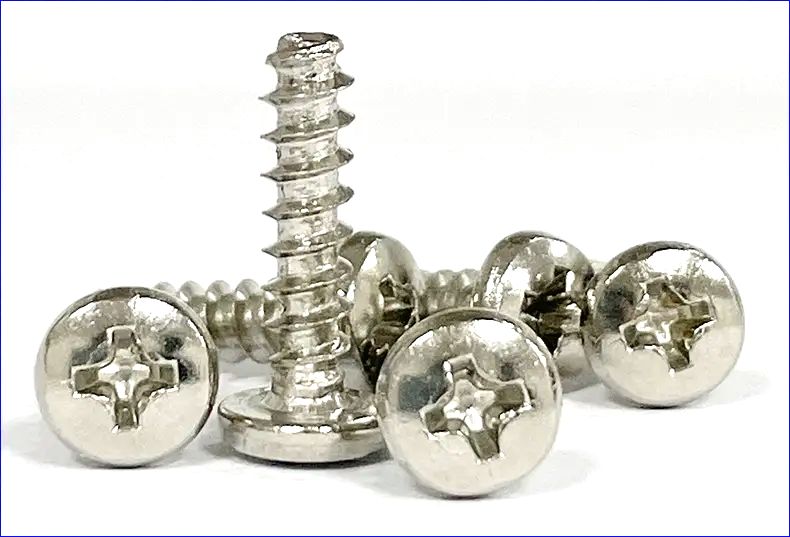
7. 溶融亜鉛めっき
溶融亜鉛めっきは、液体に加熱された亜鉛の熱拡散コーティングです。コーティングの厚さは15~100μmです。また、制御は容易ではありませんが、耐食性に優れており、エンジニアリングでよく使用されます。溶融亜鉛めっきプロセスでは、亜鉛廃棄物や亜鉛蒸気などの深刻な汚染が発生します。
コーティングが厚いため、ファスナーの内ねじや外ねじをねじ込むのが困難になります。溶融亜鉛めっき処理の温度の関係で、10.9級(340~500℃)以上のファスナーには使用できません。
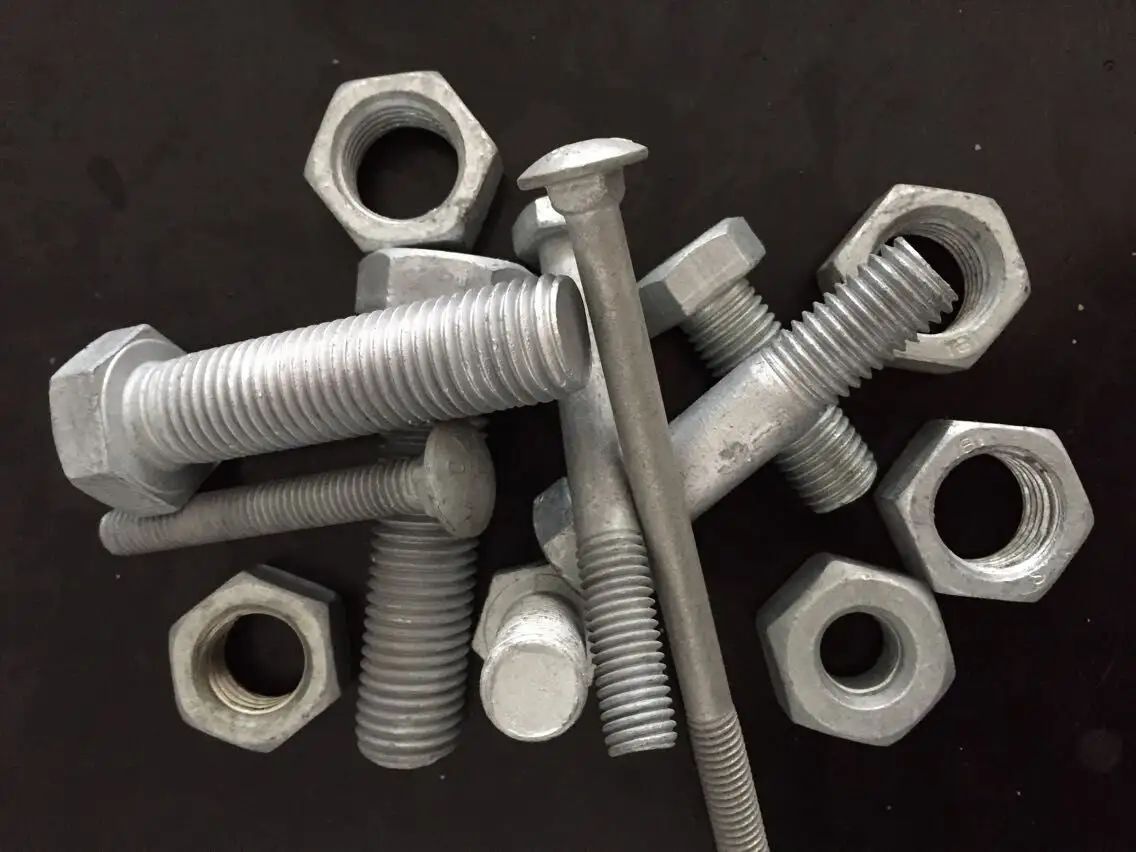
8. 亜鉛の浸透
亜鉛浸透は、亜鉛粉末の固体冶金熱拡散コーティングです。均一性が良く、ねじ部、止まり穴ともに均一な層が得られます。めっき厚さは10~110μmです。誤差は10%以内に抑えられます。下地との密着力、耐食性は亜鉛めっき(電気亜鉛めっき、溶融亜鉛めっき、ダクロメット等)の中で最高です。その加工プロセスは無公害であり、最も環境に優しいものです。
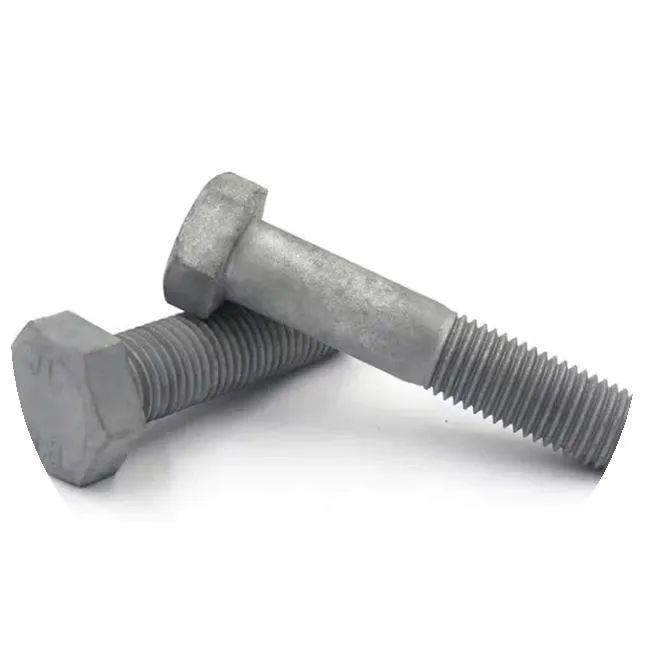
9.ダクロメット
水素脆化の問題はなく、トルク予圧の一貫性性能は非常に優れています。クロムや環境問題を考慮しなくても、ダクロメットは実際、高い耐食性要件を備えた高強度ファスナーに最も適しています。
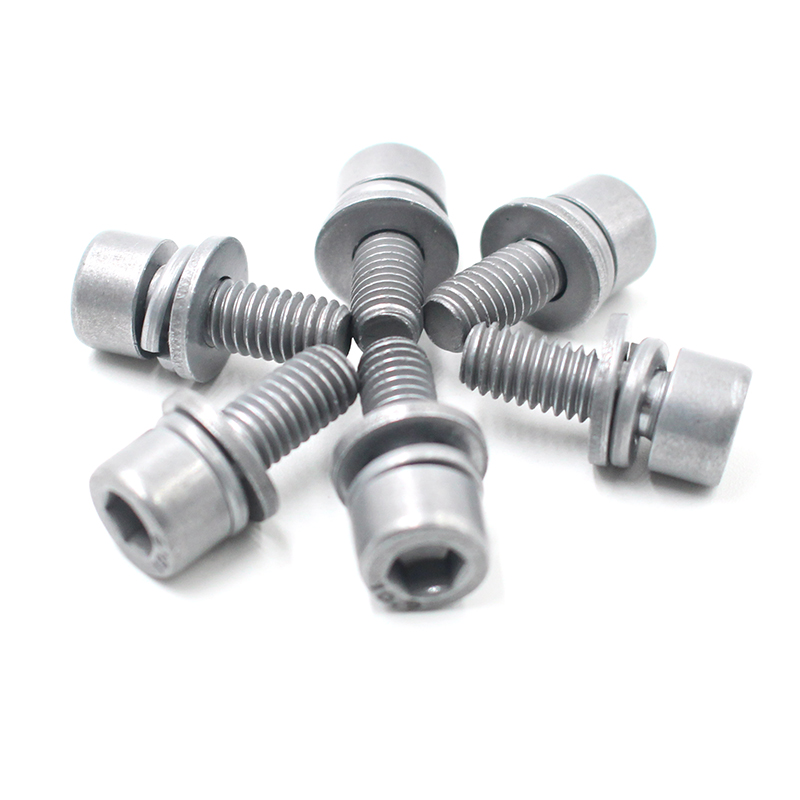
投稿日時: 2023 年 5 月 19 日